Amorphous cores are a new material that is becoming more popular due to their superior performance compared to traditional ferrite and Supermalloy cores. They have a higher Curie temperature, wider working temperature range and excellent thermal stability. They also have higher saturation magnetic flux density resulting in lower losses and higher permeability than ferrite or Supermalloy materials.
Using amorphous metal for power electronics applications allows for size, weight and cost savings. Amorphous metal is a soft magnetic material which can be formed into any shape and offers an effective replacement for ferrite and nickel supermalloy materials in many applications.
For example, a tape wound amorphous core can achieve no-load loss reductions of up to 30% versus silicon steel and can offer improved overload capacity by producing less heat than other materials. They are also suitable for boosting inductors where fringing flux is a concern.
These tape wound amorphous cores can be designed with fewer gaps, allowing them to achieve permeabilities less than 245 per cent and they are stable over a wide temperature range reducing EMC concerns. The amorphous material is also capable of producing less noise than conventional iron powder and ferrite cores.
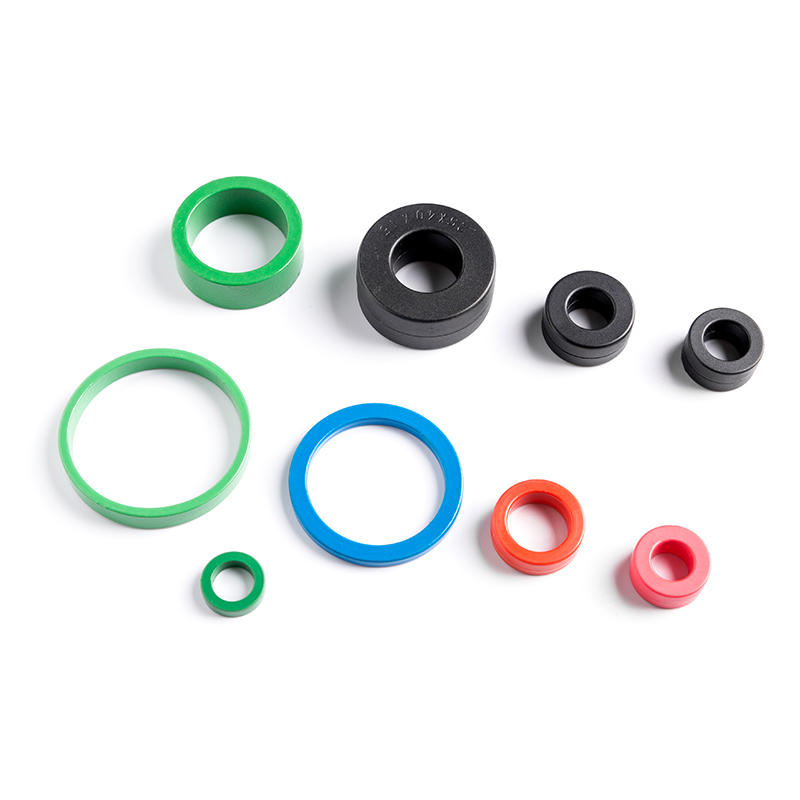
Common Mode Choke (CMC) with Nanocrystalline Amorphous Metal
These are made from an amorphous metal ribbon that is pressed into toroidal shapes. This allows for the designer to reduce size and power loss as compared to conventional solutons while still maintaining the performance required for high frequency PFC boost inductors.
Amorphous metal has a much wider operational temperature range than ferrite, making it ideal for switched-mode power supplies and other electronic systems which require high frequency. They are also more compact than ferrite and can handle larger currents without performance loss at high temperatures.
They are produced using a highly controlled annealing process that generates a nanocrystalline microstructure with grain sizes of 10nm. This improves on typical amorphous characteristics, delivering 1/5th the core loss of Fe-based amorphous metal and can be configured with a variety of BH hysteresis loops.
For example, the squareness of these hysteresis loops can be adjusted to control the magnetic properties "B-H curve shape". This enables designs that are tailored to specific applications.
During annealing, the temperature of the annealing furnace can be controlled to create the optimal B-H curve and produce a material with an outstanding combination of saturating magnetic flux density, high permeability and low magnetostriction. This results in a very robust, high-performing core that can be used for a broad range of applications including: DC Output Inductors; Differential Mode in Chokes; SMPS Output Inductors; and PFC Boost Chokes.
The amorphous core can be wound into toroidal shapes and can be configured to achieve smaller gaps than E-core ferrites, reducing fringing flux and stray field concerns. They are also suitable for boosting inductors and can be configured with a variety of gap sizes to suit the application.